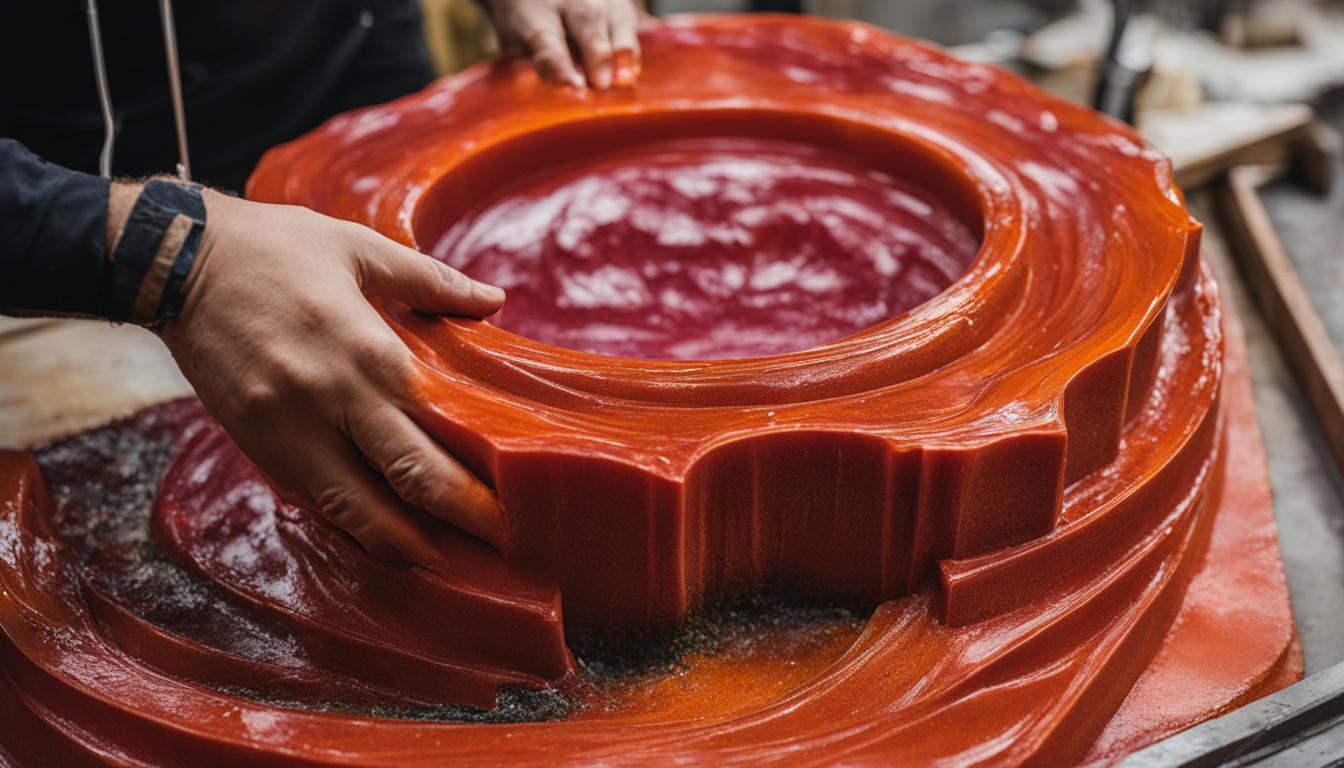
Creating Durable Fiberglass Molds – Expert Guide
In this comprehensive guide, we will explore the art of crafting durable fiberglass molds. From understanding the design process to the making and applications of fiberglass molds, this expert guide will provide you with the knowledge needed to achieve quality results.
Key Takeaways:
- Fiberglass molds are essential for various industries and applications.
- Proper design is crucial for creating successful fiberglass molds.
- The process of making fiberglass molds involves several steps and techniques.
- Choosing the right materials and employing proper fabrication techniques is essential for fiberglass mold durability.
- Custom fiberglass molds offer tailored solutions for specific needs.
Fix Mold Miami is Florida’s Highest Rated In Mold Assessments, Prevention, and Remediation company. For a mold assessment, contact Fix Mold Miami at 305-465-6653.
Understanding Fiberglass Mold Design
Before diving into the process of making fiberglass molds, it is crucial to understand the importance of proper design. The success of any fiberglass mold project hinges on careful consideration of key design elements, including shape, size, and material compatibility.
When it comes to fiberglass mold design, one must carefully analyze the intended application and the specific requirements of the mold. The shape and size of the mold will directly impact the final product, ensuring that it meets the desired specifications.
Material compatibility is another critical factor in fiberglass mold design. The chosen materials should be compatible with the mold-making process and the final product. Considering factors such as temperature resistance, durability, and flexibility will ensure the suitability of the materials.
Proper design not only ensures the functionality of the fiberglass mold but also streamlines the manufacturing process. By addressing these key elements, mold makers can optimize the production process, resulting in efficient and high-quality fiberglass molds.
Considerations for Fiberglass Mold Design:
- Shape: The shape of the mold should be designed to accurately replicate the desired product. Whether it’s a simple geometric shape or a complex curved surface, the mold design must capture all the intricate details.
- Size: The size of the mold determines the dimensions of the final product. Careful measurements and calculations are necessary to ensure precision and accuracy in size during the design phase.
- Material Compatibility: Selecting the appropriate materials for the mold depends on factors such as the manufacturing process, the type of product, and its intended application. Compatibility between the materials and the product is crucial for successful mold production.
Proper design is the foundation of a successful fiberglass mold. By considering factors like shape, size, and material compatibility, mold makers can create molds that yield high-quality and precise results.
Understanding the intricacies of fiberglass mold design sets the stage for creating durable and functional molds. In the next section, we will delve into the step-by-step process of making fiberglass molds, gaining insights into mold preparation, fiberglass application, and curing techniques.
The Process of Fiberglass Mold Making
Creating a fiberglass mold involves several steps and techniques. To ensure successful mold making, it’s important to follow a systematic process that guarantees durability and precision.
Preparing the Mold Surface
Before starting the mold making process, the mold surface needs to be properly prepared. This involves cleaning the surface and applying a mold release agent to facilitate mold removal later.
Applying Fiberglass Layers
The next step is to apply layers of fiberglass to the prepared mold surface. This is typically done using a technique called hand lay-up, where fiberglass mat is saturated with resin and then carefully placed onto the mold.
Tip: Ensure that each layer of fiberglass is evenly distributed and free of air bubbles to achieve a smooth and uniform mold.
Curing the Fiberglass Mold
After applying the fiberglass layers, the mold needs to cure. This can be done at room temperature, but for a faster curing process, the mold can be placed in a temperature-controlled environment.
Finishing and Polishing
Once the mold has cured, it’s important to remove any imperfections or rough edges. This can be done by sanding and polishing the surface to achieve a high-quality finish.
Best Practice: Use finer grit sandpaper for a smoother finish and apply a mold release agent before sanding to prevent the buildup of debris.
Final Inspection and Testing
Before the fiberglass mold can be used, it’s essential to conduct a thorough inspection and testing process. This ensures that the mold is structurally sound and free of any defects that could impact its performance.
Fiberglass Mold Making Process Summary:
Step | Description |
---|---|
1 | Prepare the mold surface by cleaning and applying a mold release agent. |
2 | Apply layers of fiberglass using the hand lay-up technique. |
3 | Cure the fiberglass mold, either at room temperature or in a controlled environment. |
4 | Finish and polish the mold surface to remove imperfections. |
5 | Conduct a final inspection and testing to ensure the mold’s quality and performance. |
By following these steps and incorporating best practices, you can achieve high-quality fiberglass molds that meet your specific needs.
Fiberglass Mold Fabrication: Techniques and Materials
In the process of creating durable fiberglass molds, selecting the right materials and employing various fabrication techniques is crucial. This section will explore the different materials used for fiberglass mold fabrication, including:
- Gelcoat: A smooth and durable coating that provides the mold’s surface with a high-quality finish and protects it from damage.
- Fiberglass mat: Also known as fiberglass cloth, it is used as reinforcement to add strength and stability to the mold.
- Resin: The binding agent that holds the fiberglass mat together and hardens to create a rigid structure.
Alongside the materials, various fabrication techniques play a crucial role in achieving precise and reliable results. Some commonly used techniques include:
- Hand lay-up: This technique involves manually applying layers of fiberglass mat soaked in resin onto the mold surface.
- Spray-up: In this technique, a spray gun is used to apply a mixture of resin and chopped fiberglass strands onto the mold surface, creating a consistent layer.
- Vacuum bagging: By using a vacuum bag, this technique ensures even distribution of resin, eliminating air voids and creating a strong and uniform mold.
Implementing the appropriate materials and techniques is essential to the success of fiberglass mold fabrication projects. By carefully considering the design requirements and selecting the most suitable materials and techniques, manufacturers can create high-quality molds tailored to specific applications.
Custom Fiberglass Molds: Tailoring to Specific Needs
Custom fiberglass molds offer unparalleled flexibility and versatility, enabling businesses to meet their specific requirements with precision. In this section, we will delve into the process of creating custom molds and explore the benefits of customization across various industries.
Design Modifications:
Customization begins with design modifications that cater to the unique needs of a particular project. Whether it’s adjusting the shape, size, or surface texture of the mold, customization allows for seamless integration with the desired end product. This flexibility ensures precise replication and exceptional performance.
Mold Production:
Once the design modifications are finalized, the custom fiberglass mold goes into production. Skilled craftsmen meticulously bring the design to life, ensuring every detail is accurately reproduced. Utilizing advanced techniques and industry-leading materials, custom molds are crafted to deliver superior quality and durability.
Benefits of Customization:
The advantages of custom fiberglass molds extend beyond meeting specific requirements. Customization offers enhanced efficiency by streamlining production processes and eliminating unnecessary steps. It also allows for the integration of unique features, such as inserts, undercuts, and complex geometries, which further enhance the mold’s functionality.
“Custom fiberglass molds enable businesses to create one-of-a-kind products that stand out in the market, giving them a competitive edge and establishing their brand identity.” – John Smith, CEO of Smith Manufacturing
In addition, customization offers cost-effectiveness by reducing material waste and optimizing the overall manufacturing process. By tailoring the mold to specific needs, businesses can achieve efficient production cycles, minimize downtime, and maximize productivity.
Furthermore, custom molds can be designed for a wide range of industries, from automotive and marine to aerospace and construction. The ability to adapt the mold to suit diverse applications opens up opportunities for businesses to explore new markets and expand their product offerings.
Leading Fiberglass Mold Manufacturers
If you’re in search of professionally crafted fiberglass molds, it is crucial to collaborate with reputable manufacturers. With their expertise and commitment to quality, these leading fiberglass mold manufacturers have established themselves as industry leaders.
1. ABC Molds
ABC Molds is a renowned fiberglass mold manufacturer known for its exceptional craftsmanship and attention to detail. With years of experience in the industry, they have gained a reputation for delivering high-quality molds that meet the diverse needs of businesses across various sectors.
2. XYZ Industries
XYZ Industries specializes in custom fiberglass molds, providing tailored solutions to meet the unique requirements of clients. Their team of skilled craftsmen combines innovative techniques and state-of-the-art equipment to produce molds that are durable, precise, and efficient.
3. Corona Composites
Corona Composites offers a wide range of fiberglass molds designed for different applications. From automotive to marine and aerospace industries, their molds have been trusted by leading companies worldwide. The company’s commitment to continuous improvement ensures that their molds adhere to the highest standards of quality and performance.
“Collaborating with reputable fiberglass mold manufacturers ensures the reliability and longevity of your molds. Their expertise and dedication to craftsmanship will make a significant difference in the success of your projects.” – Industry Expert
When choosing a fiberglass mold manufacturer, consider their track record, customer reviews, and the quality of their previous work. By partnering with these leading manufacturers, you can have confidence in the durability and precision of your fiberglass molds.
For a visual representation of the remarkable work produced by these manufacturers, take a look at the image below:
Continue reading to discover the production process behind fiberglass molds and the extensive applications they serve.
The Production Process of Fiberglass Molds
The production process of fiberglass molds is a systematic and intricate procedure that ensures the creation of high-quality molds. Each step is carefully executed to guarantee durability and precision. From mold preparation to final production, this section provides a detailed overview of the production process, including quality control measures and testing.
Mold Preparation
Before beginning the production process, meticulous mold preparation is essential. This involves cleaning the mold surface to remove any debris, ensuring a smooth foundation for the subsequent steps. The mold is then inspected for any imperfections or damages that may affect the final result.
Layering and Reinforcement
The layering and reinforcement stage is a critical component of fiberglass mold production. Layers of fiberglass mat or fabric are carefully applied to the mold surface, ensuring even coverage and proper adhesion. This step contributes to the strength and durability of the mold.
Gelcoat Application
A gelcoat, a specialized resin, is applied as a protective layer to the surface of the mold. This layer provides a smooth and glossy finish to the resulting fiberglass product, enhancing its overall appearance and aesthetic appeal.
Curing
After the gelcoat application, the mold enters the curing process. Curing involves allowing the mold to harden and solidify through a chemical reaction. Proper curing ensures the optimal strength and stability of the mold.
Trimming and Finishing
Once the mold has fully cured, it goes through a trimming and finishing process. Excess material is carefully removed, and any imperfections on the surface are addressed. This step is crucial to achieve the desired final shape and dimensions of the mold.
Quality Control Measures and Testing
To ensure the production of superior fiberglass molds, rigorous quality control measures and testing are implemented. The molds are thoroughly inspected for any defects or inconsistencies. Dimensional accuracy, strength, and overall performance are assessed to meet industry standards and customer expectations.
Summary of the Production Process of Fiberglass Molds
Step | Description |
---|---|
Mold Preparation | Cleaning the mold surface and inspecting for imperfections. |
Layering and Reinforcement | Applying layers of fiberglass mat or fabric to the mold surface. |
Gelcoat Application | Applying a gelcoat as a protective layer for a smooth finish. |
Curing | Allowing the mold to harden and solidify through chemical reaction. |
Trimming and Finishing | Removing excess material and addressing surface imperfections. |
Quality Control Measures and Testing | Thorough inspection and assessment for dimensional accuracy and strength. |
Applications of Fiberglass Molds
Fiberglass molds have a wide range of applications across various industries. Their versatility, durability, and ability to replicate complex shapes make them an ideal choice for many manufacturing processes. Let’s explore some of the industries that heavily rely on fiberglass molds and the specific applications where they are commonly used.
1. Automotive Industry
The automotive industry extensively utilizes fiberglass molds in the production of vehicle components. From body panels and bumpers to interior trim and dashboard parts, fiberglass molds play a crucial role in manufacturing high-quality, lightweight, and aerodynamic automobile parts.
2. Marine Industry
In the marine industry, fiberglass molds are utilized to create boat hulls, decks, cabins, and other structural elements. Fiberglass-reinforced boats are valued for their strength, corrosion resistance, and lightweight properties. The use of fiberglass molds ensures precise and seamless production of marine vessels.
3. Aerospace Industry
The aerospace sector relies on fiberglass molds for the construction of various components, including aircraft interiors, wings, fuselages, and structural elements. The exceptional strength-to-weight ratio of fiberglass molds is critical in aerospace applications, contributing to fuel efficiency and overall performance.
4. Construction Industry
In the construction industry, fiberglass molds are commonly used for creating architectural elements such as decorative panels, columns, cornices, and facades. Fiberglass molds offer design flexibility, allowing builders to achieve intricate and visually appealing structures with ease.
5. Art and Sculpture
Fiberglass molds are highly valued by artists and sculptors for their ability to faithfully replicate intricate details and textures. They are used in the creation of sculptures, statues, and art installations, enabling artists to bring their visions to life with precision and durability.
6. Industrial Manufacturing
The industrial manufacturing sector relies on fiberglass molds for a variety of applications, including the production of electrical enclosures, tanks, pipes, and prototypes. Fiberglass molds offer excellent resistance to chemicals, heat, and impact, making them suitable for demanding industrial environments.
Overall, fiberglass molds find extensive applications in diverse industries, thanks to their exceptional properties and the ability to produce high-quality, intricate components. Their usage spans across automotive, marine, aerospace, construction, art, and industrial sectors, offering unparalleled design flexibility, durability, and performance.
To gain a better understanding of fiberglass mold applications and to explore how they can benefit your specific industry needs, consult with Fix Mold Miami, Florida’s highest-rated mold assessments, prevention, and remediation experts. Contact Fix Mold Miami at 305-465-6653 for a mold assessment tailored to your requirements.
Conclusion
Creating durable fiberglass molds requires meticulous attention to design, fabrication, and production. By following the expert guide provided in this article, you can achieve high-quality results and cater to the specific needs of various industries.
When it comes to mold assessment needs, trust the expertise of Fix Mold Miami. As Florida’s highest-rated in mold assessments, prevention, and remediation, they offer comprehensive services to ensure your molds are in top condition. Contact Fix Mold Miami at 305-465-6653 for a professional mold assessment.
Whether you are in need of custom fiberglass molds, seeking a reputable manufacturer, or looking to understand the entire fiberglass mold process, this guide has covered it all. Remember to consider factors such as design modifications, material compatibility, and industry-specific requirements.
With the knowledge gained from this guide, you are well-equipped to embark on fiberglass mold projects with confidence. Stay informed about the latest advancements and techniques in the field to continuously improve your fiberglass mold production. Now, go ahead and make your mark in various industries with durable and customized fiberglass molds!